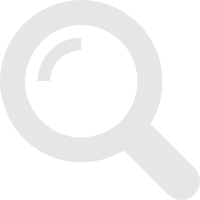
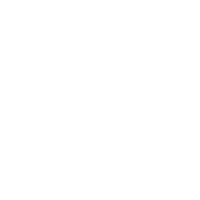
文 葛晶
丰田生产方式是个复杂系统,需要大量的资源投入来打造这个生产体系。例如,我们在工厂现场观察到,即使在生产线的配件准备区,也是高度智能化的:每种零件放置区上方的指示灯提示拣选人员该零件需要拿取的数量,拣选人员触碰指示灯开关使其熄灭,顺手取走合适数量的零件;待这个区域里的零件全部取完,该区域的打印机自动打印零件清单;拣选人员将清单与取好的零件一起送入运输区, 等待运送。从这样一个细小的环节,就可以想象整个生产体系的信息化、智能化水平,也不难推算这个体系的庞大资源投入。对于中国众多制造企业来讲,难以进行这样的投入。至少现阶段,我们不一定能学丰田的生产方式。
在信息化与智能化的华丽外表之下,是丰田管理理念决定了丰田生产方式必然是节约的、高效的,信息化与智能化只不过是这种管理理念的实现手段而已。而这种管理理念具有相当的普适性,对于众多面临二次转型的中国制造企业来讲,一定要学丰田的管理理念。
丰田的管理理念,令人颇有感触的主要有以下几个方面:
1.原材料是稀缺资源
丰田认为原材料库存与在制品是在无效占用资源,要尽可能降低原材料库存与在制品数量,实现资源利用最大化,绝不是把库存压力简单转嫁给供应商。
这种对于资源稀缺的紧迫感也许源于日本的资源匮乏和长期以来形成的民族文化; 对于地大物博的中国来讲,也许不太需要如此紧迫和焦虑。对于企业来讲,原材料库存与在制品可能算不上对稀缺资源的浪费,但是至少这样的库存与在制品占用了企业相当数量的现金流,影响了企业资金的运转效率。因此,中国企业还是需要有意识地加强管理,实现资源利用最大化。
2.时间是稀缺资源
丰田管理理念的前提假设,即时间是稀缺资源,要极力消除对时间的无效浪费。在丰田,我们随处都可以看到通过动时研究, 实现动作标准化,进而消除多余动作、实现时间利用最大化的鲜活事例。还记得上文提到的零件拣选人员取零件的动作吗?他伸出手,先触碰指示灯开关,使其熄灭,然后顺势拿取合适数量的零件;他只用一个动作, 完成两项任务,中间没有任何动作停顿。再比如,生产线上一次要取三颗螺母,如果人工取就需要花时间数数,丰田的工人们发明了磁铁装置,一次就取三个,省去人为数数和判断的时间。在中国,除了引入丰田生产方式的少数企业之外,估计很少有企业能如此关注员工的动作浪费、时间浪费吧?
我们不得不感慨,泰勒制的动时研究、最古朴的科学管理方法,在这里被应用得淋漓尽致。在丰田的课堂上,我们这群管理咨询精英亲自动手改进组装电风扇的流水线, 我们的解决方案更多侧重流程环节的重组, 基本不涉及动时研究,我们自我解嘲为动作研究需要一线工人长期的自我感知、自我优化。这是不是也从某个角度反应出我们真的不太在乎这种以秒为单位的时间浪费?
3.有标准的坚决执行,绝不擅自更改
这个理念与动时研究密不可分。通过动时研究确定的动作标准,基本接近最优了, 擅自改动一般不会提高效率,而是降低效率。也许是在人性的本能选择与自动化的压力双重作用之下,丰田人都遵守标准,绝不擅自更改。
再看国内的企业,不知道这个问题是要回归到人性还是文化层面解释。中国企业更喜欢定义结果标准化,而中间过程管理则相对粗放。员工也喜欢,别管我怎么做的, 我做出来符合你要求不就行了。作业标准化在中国推行很难。曾经有商业企业讲到停车场的卫生管理标准化问题。企业制定了明确的停车场卫生清扫标准,员工就是跟你玩猫捉老鼠的游戏,你去监督检查,他就执行, 你不检查了,他就不执行了。笔者最近碰到的一个制造企业,引进国外的制造标准开展生产制造。过程中,有些头脑灵活的员工擅自就把作业标准给改了,因为这样改他们自己操作更方便(自己投入更小),产品在外观上也没啥不同,但最后证明这样的创新对产品质量是有不良影响的。还有一个有意识的现象是,生产线上的骨干员工经过优胜劣汰,留下来的都是特别听话的,只按标准做事。这到底是好事儿还是坏事儿?……